1. Procedure for Drag & Dropping
The Drag and Drop Operation allows the user to select components in the Summary screen of Inventory Control Management and drag the items into the Integrated Bill of Material & AVL Main screen to add them as line items in the BOM.
Use this procedure as an alternative to Manually Adding Line Items to a BOM.
Open the Inventory Control Mgt. Summary screen and use Find to display the desired components.
Size the Inventory Control display by placing the cursor on the far right hand side of the display. Wait until it turns into an arrow. Holding the mouse button down, move it to the left until just the following displays:
|
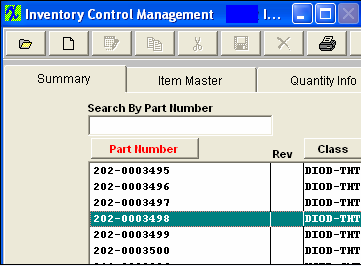 |
Open the Integrated Bill of Material & AVL BOM Main screen, position it in the lower right hand corner of the Manex screen.
Depress the Edit button and enter your password.
|
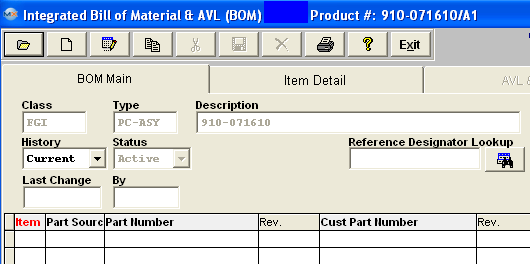 |
The following selection screen will appear:
Choose Drag and Drop.
|
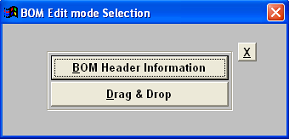 |
The following message will appear:
|
 |
Move the cursor to the Inventory window. Highlight the desired component. Use the left mouse button to select an item in the Inventory Control Management screen. Release the left mouse button. RIGHT click on the mouse button and CONTINUING TO HOLD THE RIGHT MOUSE BUTTON DOWN, move the mouse cursor over to the BOM screen. Release the right mouse button.
Note: When you drop (release the mouse button), be sure that you have the cursor over the white area,. Drag each component into the BOM in Line Item # sequence.
Enter the quantity of the part per assembly when prompted. Select the Work Center.
Type in the prefix for the Reference Designator. Type in the Reference Designator Start Number. Depress the Calculate button.
The Number and Reference Designator Fields will fill in.
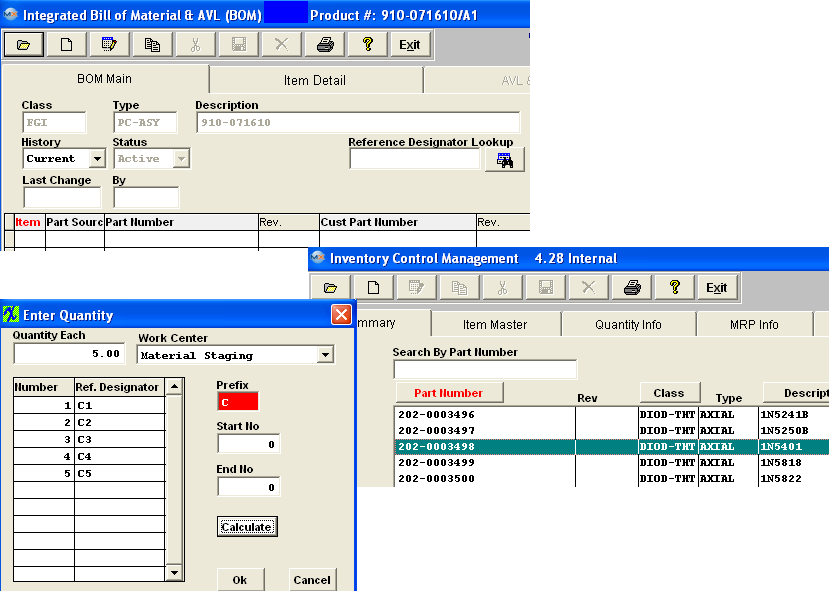
Depress the "OK" button to Save or the "Cancel" button to abandon changes. User may also click on the X button to save the changes and close the screen.
Depress the Save button in the BOM screen when finished dragging and dropping.
Depress the Item Detail tab in the BOM module. The following screen will appear:
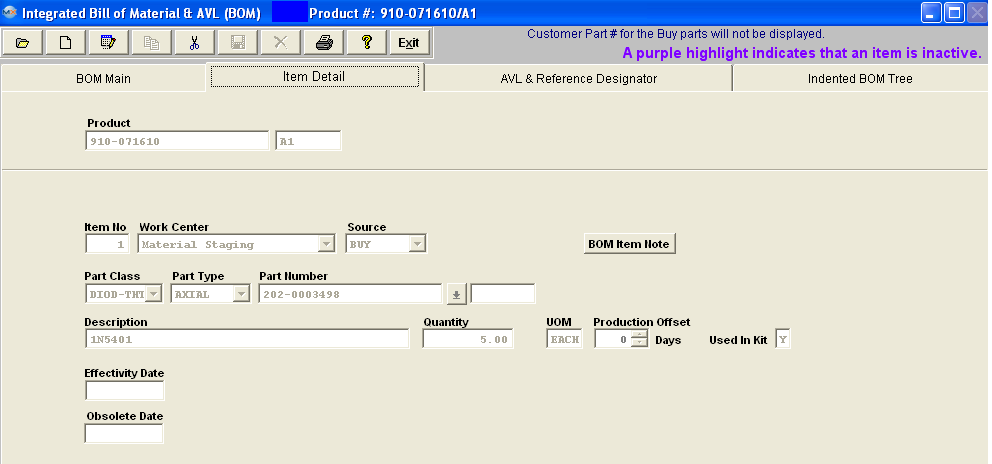
Review the detail. If you want to make any changes, depress the Edit button while this screen is open. Type in your password. You may change Item Number, Work Center, Quantity, Production Offset days, Used in Kit, and may add Effectivity Date and Obsolete Date. Depress the Save button.
All the AVL's will default in as approved and require the user to deselect as desired. If no AVL's are approved a popup will appear forcing the user to approve at least one AVL.
When the BOM for the assembly has a customer assigned to it, then ManEx will pull the approved AVL's from the customer side NOT the internal side. For example: Part “XYZ” may have several AVL’s and several different customers linked to it. Each customer may approve different AVL’s. So when the part is linked to a specific customer’s BOM only the AVL’s linked to that customer part will be displayed on the BOM as approved. The AVL screen looks at the accepted AVL’s for that customer on the “consigned” or “Customer” side of each part whether it was added to the BOM as a “BUY”, “MAKE” or “Consigned”. If no customer is assigned to the BOM then the AVL’s will be pulled from the internal side. NOTE: If "GENR" is approved on the BOM MRP will consider any inventory for that part even if the AVL is NOT approved on the BOM. For further detail refer to Article #2560 .
If you want to add alternate parts, depress the AVL and Reference Designator tab. Depress the Edit button. Enter your password. Depress the Add button next to the alternate parts section of the screen.
The following selection option will appear:
If you select Internal Part Number, then enter the Part Number into the Red Box.
|
 |
If you select Consigned Part Number, Select the Customer from the Pull Down list, then enter the Customer PN into the Red Box.
|
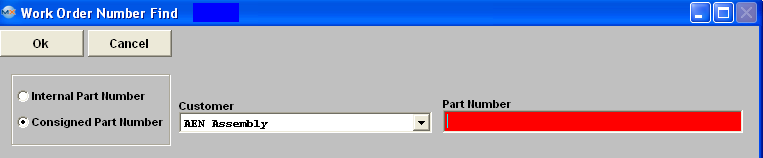 |
Information regarding the alternate part will display in the bottom section, as displayed below:
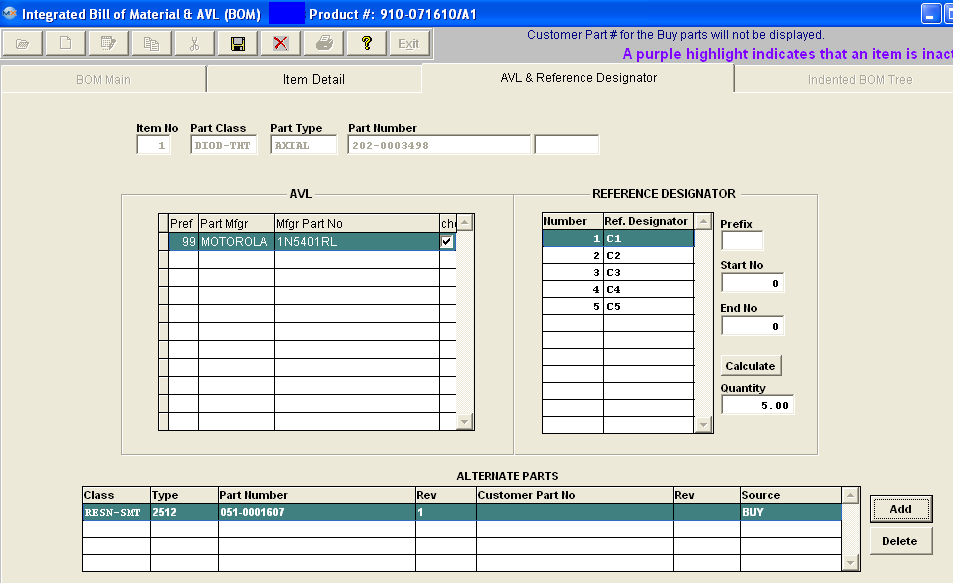
Depress the Save button.
|