This section is used to close the kit from further transactions. Once closed, no further parts may be issued to or from the work order.
NOTE: User MUST have full rights to the Kitting & Shortage Management module within Security to be able to close a kit.
NOTE: It is very important to close out all kits. Kits need to be closed manually so the user can choose whether the over-issues are to be returned to stock, or charged to the work order. If kits are not closed users are likely to have a huge manufacturing variance, or very inaccurate inventory records, and MRP will think that the over-issues are available to meet demand, when they might not actually be available.
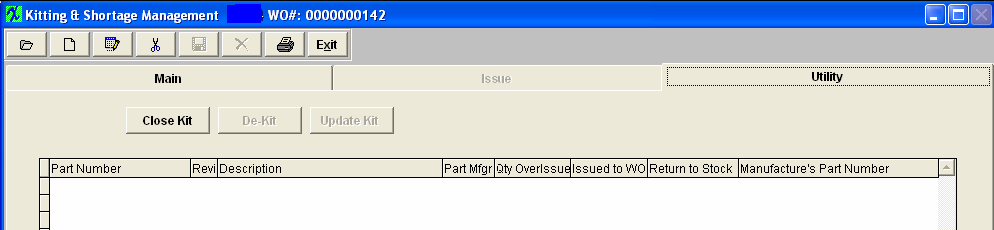
Once the Close Kit button has been depress the following screen will appear, this screen will list all over-issues for disposition, if the parts still have other locations available, the code only lets the user return back to those locations. The system will list all the available locations for the same manufacturere but not "WIP", "WO-WIP" and "MRB" locations for user to return. It will only "un-delete" a location if NO other locations are available. It defaults all items to have the over-issue qty returned to stock to the default warehouse. If the user choose to return all inventory to stock they just have to click the "OK" button. If they choose to assign all the over-issued qty to the Work Order (kit) they can do so by depressing the "Issue All to Kit" button, and the pick qty will increase to include the overissued qty. So, if the users decide to re-open the kit, they have the option to return the material back to inventory if they choose.
NOTE: If the user REDUCES the Build Qty on a Work Order that will change the WO status to "CLOSED", upon closing the kit the system will take the original quantity pulled to the kit and automatically cost the different to the kit without giving any option to the user. If the user does NOT wish to have the extra parts automatically costed to the kit upon closing they will need to change the WO status from "CLOSED" to "STANDARD", return to the Kitting module and "UPDATE" the kit, then return to the WO module and edit/save the record without making any changes – the Status will automatically update to Closed. See attached word document <<PS_961_090427.docx>> for an example.
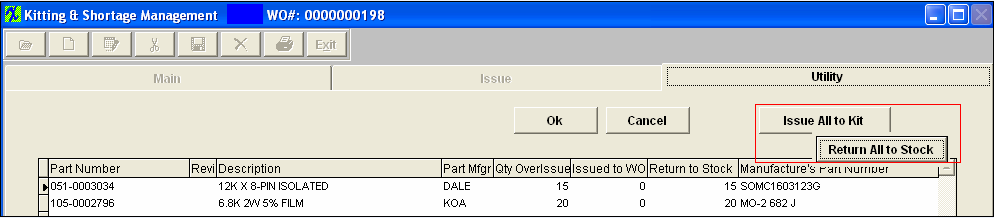
The act of closing the kit sets up the material variance entry for the accounting module if more parts or less parts than called for by the Kit for the Bill of Materials and actually used.
The manufacturing variance is based on what should have been kitted according to the BOM extension for kitting for the work order. Under issues, overissues and alternate parts are considered as variances.
The BOM may contain components which may have a scrap percentage associated with them. When the standard cost is calculated for such a BOM, and if the extended quantity calculated for scrap percentage for a component is fractional, the fraction of a cost is used in the determination of the standard cost. (For example,if a component had a scrap percentage of 3%, and the BOM calls for 50 components per assembly, the cost is determined based on 51.5 components. However, when kitting the assembly, it isn't possible to issue 51.5 components, so it is rounded to 52 components. Then when the assembly is removed from WIP, and the kit is closed, the WIP is credited for the value of the assembly, which includes the price based on 51.5 components. That leaves the cost of 1/2 of the affected component left in WIP. The rounding variance tracks down these differences and also removes the remaining cost of 1/2 component.
The Line item shortages are considered as in the WIP account all the way through until the Kit is closed within the Kitting module. Upon Closing the kit within the Kitting module the Line Item Shortages are then costed out and credited out of WIP account and debited in the Mfgr Variance account. So the “Inventory WIP Valuation Report” by Work Order by Standard Cost does not deduct those line item shortages as the product is moved into FGI. For further detail see Article #3053 .
1. If no G/L account number has been established for the rounding variance user will receive the following message and a G/L account number will need to be established for the rounding variance in Inventory Setup before user can continue.
The Kit Closing Procedure will separate out the manufacturing variance, rounding variance, and the changes to WIP values.
If a part is allocated to a Work Order or a Project (linked to the work order), when the KIT over-issues to WO-WIP location. Once the WO is closed, and user chooses to return stock, the WO allocation will be cleared, but the Project allocations will be retained and carry back to stock as still allocated to that project.
If Lot Coded parts have been over-issued to the kit those over-issued parts are moved to "WO-WIP" location and the system will save what lots they were pulled from. When the Kit is closed, the kit finds all the" WO-WIP" locations and lot information, and returns the parts back to the original lot. If the lot is deleted (due to the lot qty is 0), the system will re-create that lot.
When closing a kit see Article #1777 for further detail on how Line Item Shortages are handled.
Upon attempting to close a kit, some users may report this type of message that was presented to them. This more than likely indicates that parts that have been used on the kit are currently in an active Cycle Count or Physical Inventory. Make sure that Cycle Count or Physical Inventory have been posted to Inventory and then attempt to close the kit again.
What are the actions that would cause a work order to appear on the “Kits to Close” report?
The action that causes a work order to appear on the Kits to Close report is when the Work order is closed. (In the Shop floor tracking module, the units are transferred to the Finished Goods work center). There is no longer a balance due on the order but the work order has not yet had the kit closed.
There are two aspects of closing a work order activity – 1, closing the work order; and 2, closing the kit.
The work order closes when all of the scheduled parts are either in finished goods or scrap. This happens automatically when the last transfer is made in the shop floor tracking module.
The kit closing is a manual function. It is separate, because even though the work order may be closed, somebody may not have completed kitting all the parts to the work order, nor moved all of the over-issue out of the work order. These actions are prompted for when the kit is closed. The user may close the kit without addressing the open issues, but if that happens, each will become a variance within accounting. Unfilled shortages will become a positive variance and overissued parts will become a negative variance.
It is good practice to have someone in accounting and/or inventory review the Kit to Close report and clear them out.
|