Update/Create Records Tab |
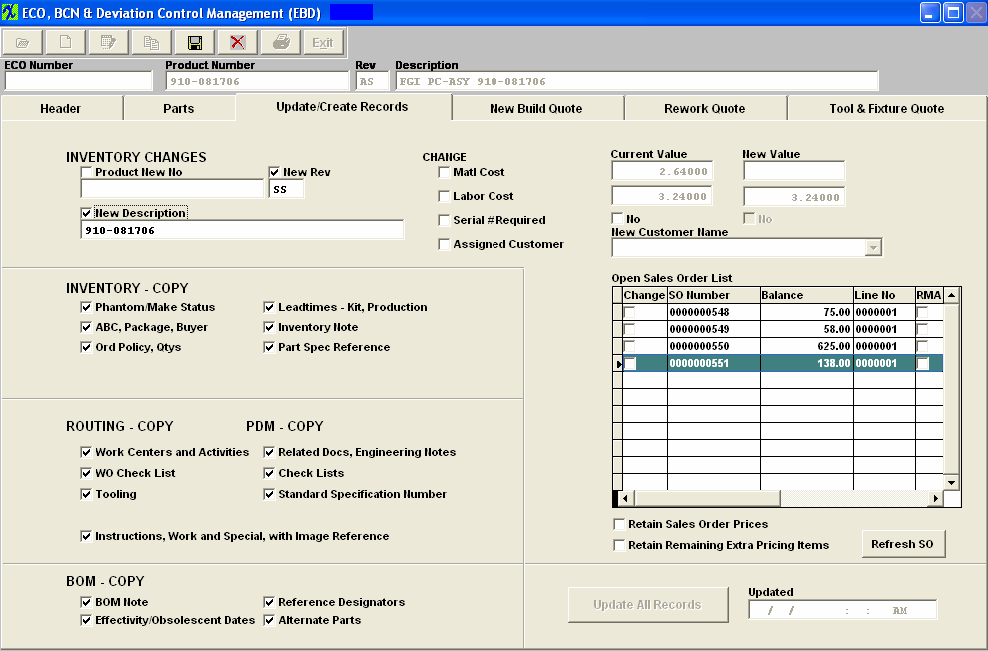
Update/Create Records Tab Field Definitions - This tab displays the revised product number, description, changes in Standard Cost, Labor Cost, whether serial number is required and updates for Engineering Change Orders only. Note: This tab is not available for Deviations or BCN.
Inventory Changes section:
Product New No: |
If the check box is checked, a new product number may be entered here.
|
New Rev: |
If the check box is checked, the new revision character may be added here.
Note: that either a new Product No or Rev has to be entered in order for the system to allow the user to save the ECO record – this check has been added to prevent any duplicated inventory records within the system. See Article #3062 on why the customer part number or revision is not updated at the same time.
NOTE: When product is changed through ECO module the same material type will be carried fwd for the next/new product at the part level but not at the AVL level.
|
New Description: |
If the check box is checked, a new description may be entered.
|
Change section:
Matl Cost |
If this box is checked, the material cost for the product will be updated based on the changes made within the Parts Section and the inventory part standard cost. |
Labor Cost |
If this box is checked, the new Labor cost for the product will be updated based on information entered within the ECO New Build Labor Cost section. |
Current Value |
The mat'l or labor cost currently existing for the product within the Inventory Control Module. |
New Value |
The revised mat'l or labor cost for the product. |
Serial # Required |
If box is checked, user then has the option of checking the "YES" or "NO" box to the right for this part to be a serialized part or not. |
No/Yes |
If the serial box is checked you have an option to check Yes or No to require the revised product to be a serialized part or not. NOTE: This box will remain NO until checked then it will update to YES. |
Assigned Customer |
This will allow the user to Assign a new Customer to the BOM. NOTE: This field is only editable if there are NO open Sales Orders or Work Orders linked to this product. |
New Customer Name |
If the Assigned Customer box is checked, user may select a customer from the pull down.
Note: Customer name can be changed on the BOM for the product only if either the Product number or revision and the product has no consigned parts for another customer nor any make/phantom parts that are assigned to another customer, and the product is not a sub-assembly for another product.
|
Open Sales Order List |
Shows all SOs (with any status except for cancel) and RMAs with this assembly number, Balance and item number. The selected SOs and RMAs will be updated with the new Product number and/or Rev number and/or Description shown upper left corner.
Note: If there have been no items shipped against the sales order selected then the system will just replace the existing product with the new within the Sales Order.
If shipments have been made against the item the old line item will be have the Ord Qty updated to equal the total Shipped and the status changed to Closed.A new line item will have been create for the new Product/Rev for the remaining balance that was left on the original item.
|
Retain Sales Order Prices |
Check this box only if you want the Unit Price to remain the same. |
Retain Remaining Extra Pricing Items |
Check this box only of you want the extra pricing to remain the same. Note: If you don't check "Retain Sales Order Prices"checkbox, then for either part itself or extra price item, no price will be updated. The "Retain Remaining Extra Pricing Items" is for adding extra items only, for the "price" column, it's still controlled by "Retain Sales Order Prices" checkbox. |
 |
“Refresh SO” button has been provided so the user can refresh the Sales Order list to check for any new SO created in the system since the ECO was first created.
|
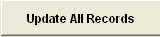 |
This button is depressed to update all records within the system based on the selections made. |
The rest of this screen comes up with all of the boxes checked for copying the revisions into the Inventory Master, Production Routing, Product Data Management and Bill of Materials. If the user does not want the assembly copied, the box will be unchecked.
|
|
|
|
|
Article ID: 1742 |