Enter System Setup/Production/Shop Floor Tracking Defaults Module |
|
The following screen will appear:
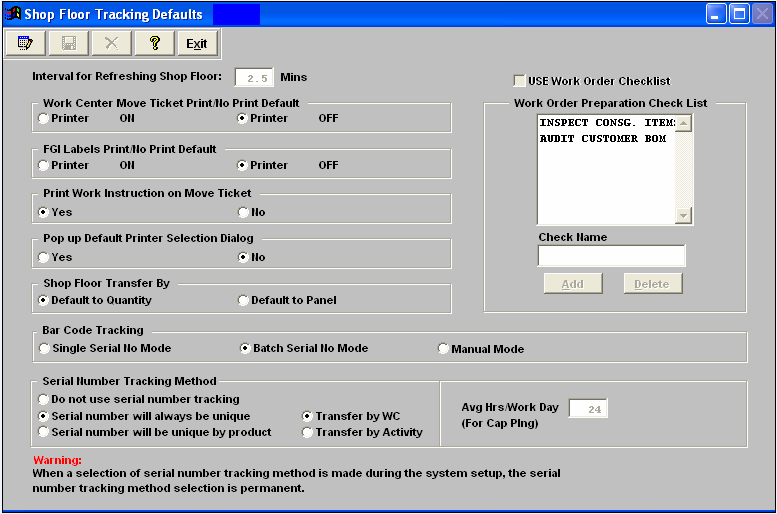
The user may edit any of the defaults by clicking on the Edit button and selecting the default to be changed. Check List items may be added by clicking on the Add button and entering the description of the item to be listed.
Use Work Order Check List
User MUST check this box to activate the Unreleased Work Order List module.
Serial Number Tracking Method can NOT be changed once a selection has been made at the beginning of a ManEx implementation. THIS DECISION, ONCE STARTED, IS IRREVOCABLE. The decision to be made is:
1, Do NOT use Serial Number tracking. If this box is checked users will NOT be allowed to check the serialized box within the ICM module, and they will receive a warning message.
2, Serial Number will always be unique. This will insure that a serial number is unique throughout the company; (meaning once used, can NEVER be used again, no matter what product).
3, Serial Number will be unique by Product. This will allow duplicate serial numbers to be used throughout the company, but they must be unique for a given product, (can be used for other products, but never again for the same product).
If Serial Numbers are NOT to be used, then the option will NOT appear when creating new part numbers within the ICM module.
If Serial Numbers ARE used, then the user will have the option when creating parts within the ICM module to either serialize the part or leave it unserialized.
If Serial Numbers are used on a part, then the user MUST enter Serial Numbers in order to move product through the SFT for shipment.
The user will also need to define whether Serial Numbers are to be transferred by Work Center or by Activity within a Work Center.
When the user has completed the changes they must press the Save or Abandon button, before exiting.
Where Used: In all shop floor functions for a product’s work orders.
Mark as Completed in RoadMap Section B Item 3
|