MRP Tab (Material Requirements Planning Info Tab) |
This Tab displays the screen in which Material Requirements Planning parameters are entered, edited or viewed. Default choices for each of these fields may be selected in System Setup Inventory Part Class Setup.
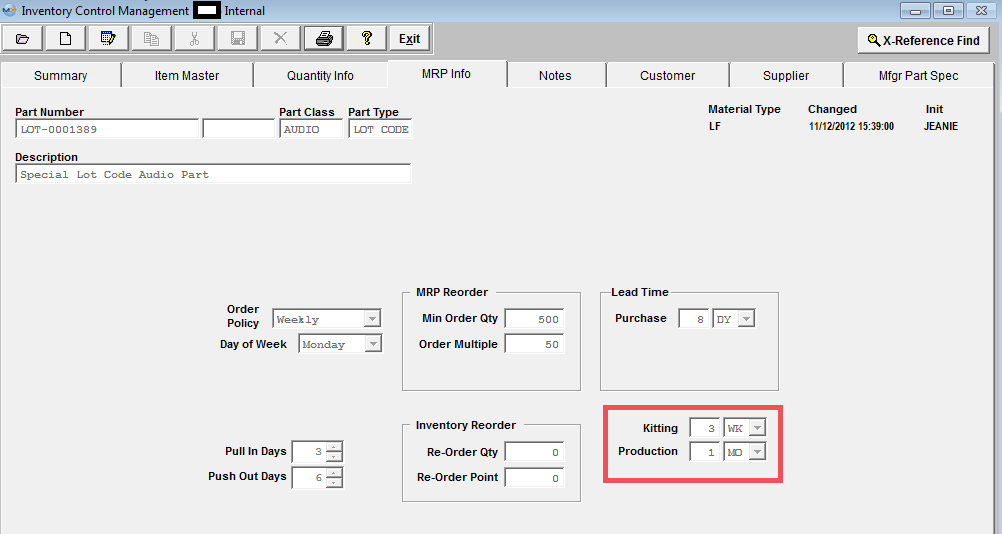
Header Information fields
Part Number, Part Class, Part Type, Description, and Material type are Item fields which repeat at the top of all Tabs to display the selected Item.
Note: All lead times are calculated with the Production Calendar.
Order Policy field |
This field is used to select the method used by the Material Requirements Planning module to combine requirements for this item in creating Planned Purchase Orders (PO’s). For instance if the choice is “Lot for Lot”, for a BUY part, the Material Requirements Planning module will plan one PO per requirement or if you select Daily then it will plan one PO for the total requirements on a daily basis. If the choice is "Lot for Lot" for a MAKE part MRP will calculate off of each Sales Order individually . If the choice were “Weekly”, for a BUY part, the Material Requirements Planning module would combine all the requirements each week and plan one PO on the first requirement day for the entire week’s needs, etc. Note: If order policy is left blank "Lot For Lot" will be used upon default for MRP calculations.
|
Min Order Qty field |
This is smallest number of the item that can be ordered from the supplier in one PO. For instance, Surface Mount components on a reel usually have a minimum order of 1000 items or more. (This field is calculated off of the Stock UOM).
|
Order Multiple field |
This field defines the even multiples of the Unit of Measure in which an item must be purchased. For example, 16AWG Wire might be only available in even hundreds of feet on a spool in which case the Material Requirements Planning module would plan a PO for the next higher even hundred above the requirement. (This field is calculated off of the Stock UOM). |
Purchase Lead Time field |
This field will be displayed for a Buy part or a Make with Make/Buy Flag part. Purchase of all items other than In-Store items requires that the PO be placed a minimum number of days before the actual requirement. This Lead Time requirement is what tells the Material Requirements Planning module how many days before a requirement to plan a PO. Changing the leadtime of a Buy part will NOT change the due date in MRP, only the date to take action. For more detail see diagram shown below. |
Kitting Lead Time field |
This field will be displayed for a Regular Make part or a Make with Make/Phantom Flag part. This Lead Time requirement is what tells the Material Requirements Planning module how many days to allow for kitting. Changing the kitting leadtime of a Make or Make/Phantom part will change the due date in MRP. A TRUE phantom does NOT require any lead times and should be left blank. BUT . . . if for some reason you need to add a lead time for a TRUE phantom ManEx does have the capability. For more detail see diagram shown below.
|
Production Lead Time field |
This field will be displayed for a Regular Make part, a Make with Make/Phantom Flag part or a Straight Phantom part. This Lead Time requirement is what tells the Material Requirements Planning module how many days to allow for production. Changing the production leadtime of a Make or Make/Phantom part will change the due date in MRP. A TRUE phantom does NOT require any lead times and should be left blank. BUT . . . if for some reason you need to add a lead time for a TRUE phantom ManEx does have the capability. For more detail see diagram shown below.
NOTE: Once the parts have been pulled to the kit and the kit status is changed to "Kit in Process" MRP is designed to calculate from the Kit Shortage and production lead time NOT from the production offset lead times. Once the parts have been pulled to the kit, the system is assuming that the shortages are needed by the WO due date, rather than the Production offset lead time, so MRP then calculates using the production lead time and due date of the WO as the date the materials must be on hand, MRP no longer takes the production offset lead time into consideration.
|
Pull In Days field |
When PO due date is more than this number of days too late for a Material Requirements Planning module requirement, a PO Due Date change Action Notice will be generated. It allows the user to have the flexability for SO and WO due dates to be different without MRP actions being generated. For more information on how the Pull-in days work within MRP see Article #2557. Note: These parameters may be thought of as filters for MRP Order Actions when the requirement dates for the parts changes. In the case of the customer pulling forward their required date, it is a greater imperative that the work orders (thus the assembly) be pulled in to match the earlier due date. So the assemblies should probably have a minimum number of days to be sensitive to earlier demands. See attached Document <<pullin-pushout discussion.docx>>.
|
Push Out Days field |
When PO due date is more than this number of days too early for a Material Requirements Planning module requirement, a PO Due Date change Action Notice will be generated. Example: if there is a PO that is due to be delivered Dec 15, but now it is not needed until Dec 26 and the Push out is 30 days, then there WOULD NOT be a message issued within MRP to reschedule the PO delivery, because it is within 30 days, but if the Push out was 5 days then an action message WOULD BE issue to reschedule the delivery because the new date was outside of the push-out days. It allows the user to have the flexability for SO and WO due dates to be different without MRP actions being generated. For more information on how the Push-out days work within MRP see Article #2557. Note: These parameters may be thought of as filters for MRP Order Actions when the requirement dates for the parts changes. The Push Out value (in days) is the number of days that the required date, base on MRP, may be pushed out (required later than the original date) but will not result in a change order to move the required delivery for the item involved. See attached Document <<pullin-pushout discussion.docx>>.
|
Re-Order Point field |
To use the Re-Order Point and Re-Order Qty rather than Material Requirements Planning for reordering this item, enter the quantity at or below which the item should be replenished. Print the "Inventory Material Reorder List" report to show items which have dropped below re-order point minimums. NOTE: The Re-Order Point/Qty fields have NO AFFECT on MRP at all. MRP will NOT consider these fields for any calculations (these fields have no connection with MRP). These fields are intended to control stock on overhead items.
|
Re-Order Quantity field |
To use the Re-Order Point and Re-Order Qty rather than Material Requirements Planning for reordering this item, enter the quantity of the re-order here. Print the "Inventory Material Reorder List" report to show items which have dropped below re-order point minimums. NOTE: The Re-Order Point/Qty fields have NO AFFECT on MRP at all. MRP will NOT consider these fields for any calculations (these fields have no connection with MRP). These fields are intended to control stock on overhead items. |
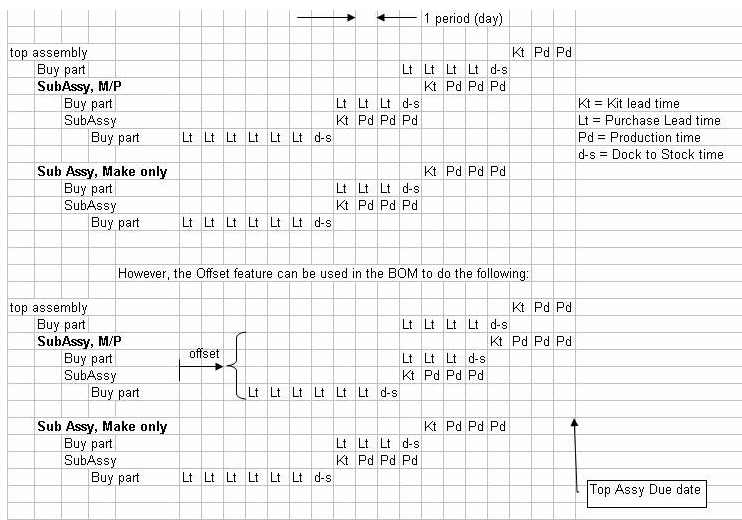
|
|
|
|
|
Article ID: 4040 |